The TMEH 1 OilCheck detects and measures the dielectric constant of oil. By comparing the measurements obtained from used and unused oils of the same brand, the SKF OilCheck is able to determine the degree of change in the condition of the oil. Dielectric change is directly related to the degradation and the contamination level of the oil and will allow the user to achieve optimised intervals between oil changes and detect increased mechanical wear and loss of the oils lubricating properties. To facilitate trending the instrument is equipped with a numerical read-out.
NOTE: The SKF OilCheck Monitor is not an analytical instrument. It is an instrument to detect only changes in the oil condition. The visual and numerical read-outs are purely a guide to enable trending of the comparative readings of a good oil to a used oil of the same type and brand. Do not rely solely on numerical readings.
Applications:
- Diesel Engines
- Gasoline Engines
- Natural Gas Engines
- Natural Gas Turbines
- Automatic Transmissions
- Any other equipment using petroleum or synthetic lubricants
Features:
- Shows changes in oil condition affected by such things as:
- Water content
- Fuel contamination
- Metallic content
- Oxidation
- Hand held and user friendly
-
Numerical read-out to facilitate trending 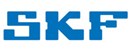
Technical data |
Suitable oil types
| mineral and synthetic oils
|
Repeatability
| better than 95%
|
Read-out
| green/red grading + numerical value (-999 to 999)
|
Battery
| 9V Alkaline IEC 6LR61
|
Battery lifetime
| > 150 hours or 3 000 tests
|
Dimensions
| Instrument: 250 x 95 x 32 mm (9.8 x 3.7 x 1.3 in.)
Carry case: 530 x 85 x 180 mm (20.9 x 3.4 x 7.0 in.)
|
Weight
| Instrument: 385 g (14 oz)
Complete in carry case: 1,2 kg (2.6 lb)
|
What
does the SKF OilCheck TMEH 1 measure?
The SKF
OilCheck TMEH 1 measures the change of the dielectric constant of oil. As a
consequence of contamination (by water, metal particles or dirt particles) and
by electrochemical changes (oxidation) that occur in oils, the dielectric
constant of the oil changes. This change in dielectric constant can be used as
an indication and sometimes a measure of deterioration of oil. The effect of
the individual contaminants and electrochemical changes is discussed below.
Water
and engine coolant:
The dielectric constant of a mineral oil is typically 2.1 and the dielectric
constant of water is typically around 60, depending on the temperature, which
is about a factor 30 higher than the oil. This means that contamination of the
oil with water or engine coolant will cause a rapid increase of the dielectric
constant of the mixture. Generally a level of 1000 ppm water or higher in oil will
lead to a significant increase of the dielectric constant.
Oil
oxidation:
Oil oxidation, or depletion of antioxidant additives, will lead to a gradual
increase of the dielectric constant of the oil.
Metal
particles:
Metal particles are conductive and will lead to a strong increase in the
dielectric constant. As the metal particles are polar, they will not stay in
the oil, but move to the sensor surfaces. This can show as a step-wise (small
jumps) increase of the reading during the measurement.
Dust
particles:
Dust
particles in oil will lead to an increase in the dielectric constant of the
oil. Generally dust levels of ISO 19/16 or higher will lead to a significant
increase of the dielectric constant in oil.
Fuel:
Fuel is difficult to detect because the dielectric constant of petrol or diesel
fuel is very close to the dielectric constant of mineral oil. Fuel
contamination does normally cause a slight decrease of the dielectric constant
and can hence hide other forms of dilution (such as by water).
The
increase of dielectric constant is usually not proportional to the degree of
oil deterioration. At larger degrees of deterioration and pollution, the
dielectric constant will not increase much more.